FLIR works with Instrumental to accelerate New Product Introduction and enhance product quality.
FLIR announced the third-generation FLIR ONE and the FLIR ONE Pro thermal camera smartphone accessories at CES 2017. The product was redesigned from the ground up to incorporate improvements in thermal imaging technology and mechanical functionality. With support from the Instrumental System, FLIR was able to rapidly bring the next-generation, high-quality product and a new factory up to speed while simultaneously lowering implementation cost.
The Challenge
Among other improvements, the third-generation FLIR ONE and FLIR ONE Pro feature all-new housing designs which include FLIR’s patent-pending OneFit™ adjustable connector, allowing the device to fit over most phone cases. The FLIR ONE Pro also features VividIR™, giving it the highest thermal image quality and clarity of all FLIR ONE generations, and a 1.8-meter drop test rating.
These new product features increased the product’s design and manufacturing complexity. As an additional variable, the FLIR team developed the FLIR ONE and FLIR ONE Pro with a factory partner with limited experience in final-product assembly. Bringing up a new factory team increased the risk of delays and initial quality. The development team at FLIR needed to work closely with the factory team as the FLIR ONE made its way through development, but wanted to do so efficiently and without co-locating staff for extended periods of time.
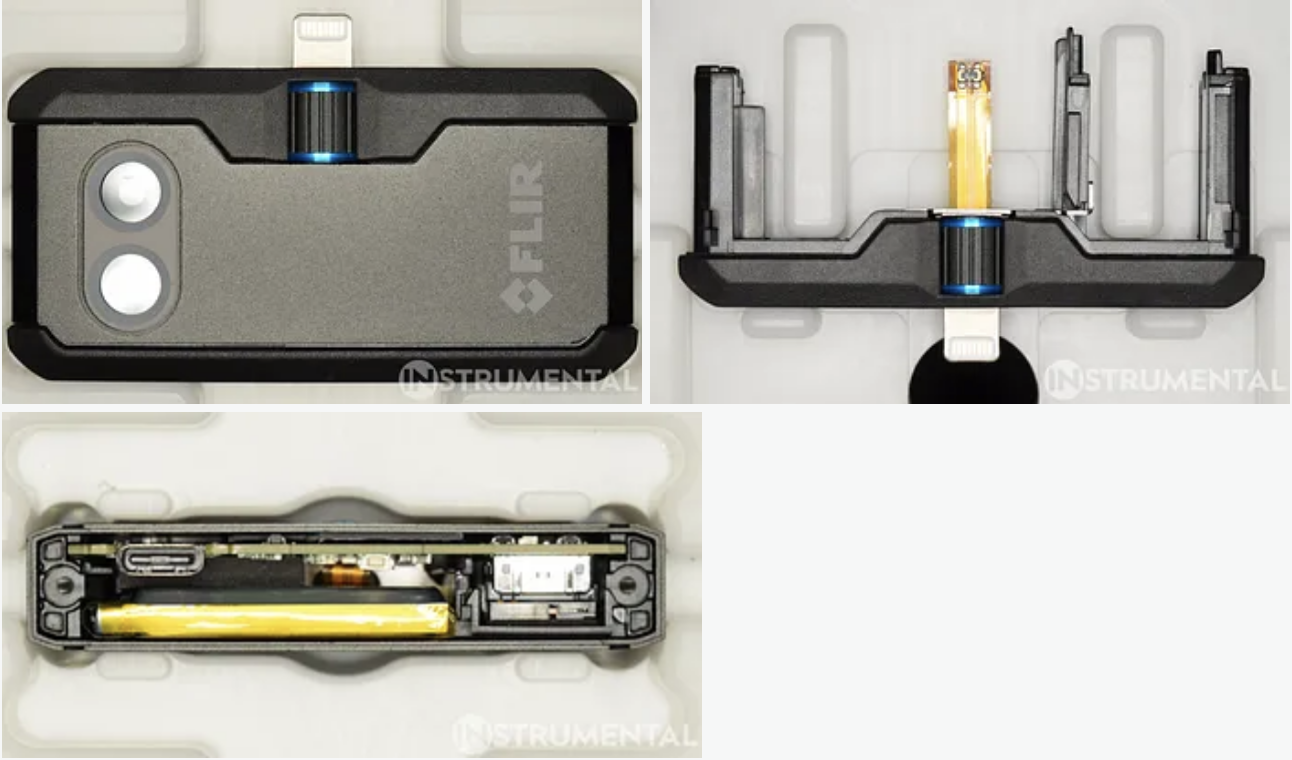
The Solution
Teams from FLIR and Instrumental worked together to set up multiple Instrumental stations on the DVT assembly line, which were configured to capture images of critical states of the product assembly process. The setup process was complete within two days, and within minutes of turning the system on, images were available for remote access to the FLIR development team. The value of the system was recognized instantly.
“Without the immediate data collection and subsequent analysis, we would not have found and solved the issues on time. Some of the issues we may never have found. I am very happy to have Instrumental on the line.”
- MARCEL TREMBLAY, DIRECTOR OF MECHANICAL ENGINEERING
- Quick Checks: Starting with the first onboarding and user training session, FLIR was able to confirm the configuration of a key part that had already been built into units, saving time and effort immediately.
- Issue Discovery and Failure Analysis: FLIR used the system to find PCB issues, discover places where components were being mis-assembled or were falling out of alignment, and track build progress.
- Unexpected Mechanical: The Instrumental system helped detect and identify unexpected mechanical issues, including an instance when a screw was not properly fastened on a critical component. This detection enabled the team to take action right away, leading to an update on all subsequent assemblies.

The image on the left shows an improperly fastened screw that Instrumental helped detect; on the right is a normal unit.
- Quality: As the FLIR team moved through development, they used the Instrumental System to discover assembly issues such as unsnapped components and part contamination and to resolve them before production. Instrumental’s data record pinpointed exactly which units were affected by key issues and shared that information with teams at the factory.
- Extended Remote Access: At FLIR in Santa Barbara, multiple cross-functional teams took advantage of the enhanced failure analysis capabilities provided by the Instrumental System. At multiple times during development, four separate conference rooms filled with different parts of the development team were working with images from the Instrumental System.
The Results
The team at FLIR brought their new product and their new factory into mass production with increased speed, lower cost, and higher quality. Throughout development, the Instrumental System gave the team what they needed to find, fix, and monitor issues. With data stored on every assembly, the data record was used to immediately show pictures to the factory, so they knew exactly what to address. Travel to the factory was reduced by 75% for some of the FLIR development team because of the Instrumental stations.
“Did we improve the quality of the final product with the Instrumental system? The answer is yes!” said Marcel Tremblay, Director of Mechanical Engineering. “Without the immediate data collection and subsequent analysis, we would not have found and solved the issues on time. Some of the issues we may never have found. I am very happy to have Instrumental on the line.” The FLIR team kept Instrumental stations on the line into mass production and continues to use Instrumental to monitor the production of every new FLIR ONE unit made.