Lenovo, P2i, and other electronics leaders deploy Instrumental’s platform to execute on continuous design and process optimization in development and production
PALO ALTO – 19 Nov, 2020 – Instrumental Inc., leader in AI-based issue detection and monitoring for electronics brands, today announced the launch of its end-to-end Manufacturing Optimization Platform with new core capabilities. Instrumental’s platform now supports the end-to-end manufacturing optimization workflow, from AI-driven issue discovery and tools for failure analysis, to ongoing real-time monitoring and continuous improvement.
Instrumental customer Lenovo is already using the platform to optimize production for their ambitious Motorola Razr program, achieving approximately $1 per unit savings and reducing production rework by nearly half. Another Instrumental customer, waterproof nanocoating provider P2i, reported a 300% increase in engineering productivity after implementing Instrumental to analyze and fix issues.
The major additions to the Instrumental platform are:
- Discover AI, Instrumental’s proprietary algorithms that search every unit produced at every key assembly stage and automatically surface a ranked list of anomalies off the line, daily. It trains with fewer than 30 golden units and does not need examples of defects to get started.
- Instrumental Data Streams which enable Instrumental customers to automatically load additional product data such as functional test results or measurements from third-party systems into Instrumental. This delivers a truly complete data record of each unit, enabling engineers to correlate anomalies from different systems easily and leverage Instrumental’s visual record to complete failure analysis in record time, and while fully remote.
By ingesting product data from across the existing test stations and systems, Instrumental now enables teams to find correlations and solve even their toughest manufacturing issues in considerably less time.
“Instrumental’s vision is to enable assembly lines that actually improve themselves continuously over time, and today’s release is a huge step toward that goal,” said Anna-Katrina Shedletsky, Instrumental Inc. CEO and founder. “By creating an AI that can proactively identify and categorize new issues faster than a human could, we’re able to take one of the most time-consuming and frustrating parts of product development from weeks or months down to days.”
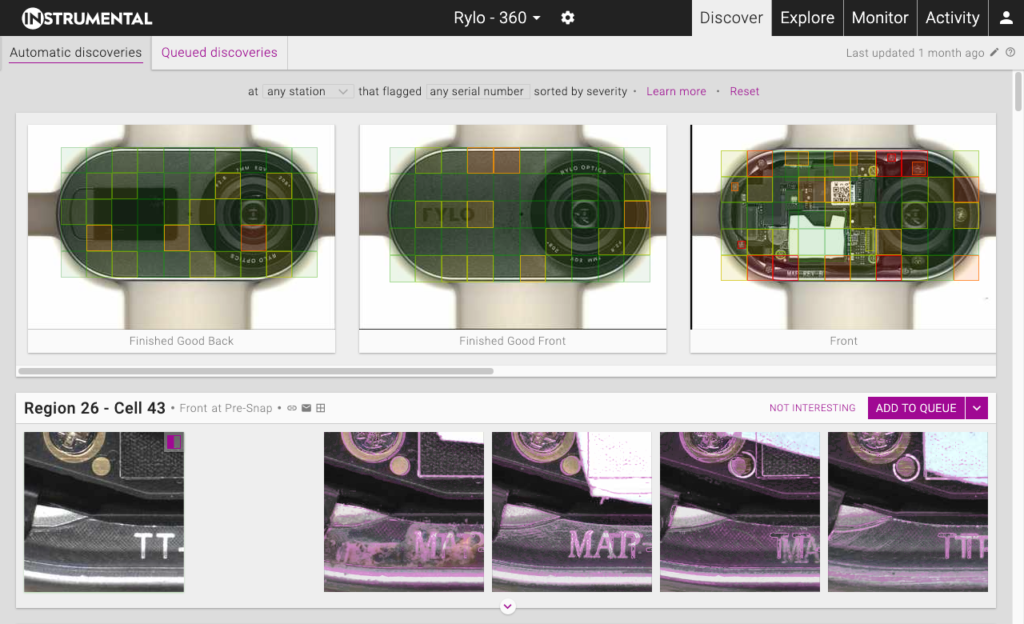
Instrumental Discover AI delivers a daily queue of anomalies automatically organized by region, with photographic examples.
Defining a new standard for Industrial AI
Artificial intelligence has been applied to manufacturing for decades, but despite the promise of Industry 4.0 and Smart Manufacturing, most solutions still fall short. This is exemplified by how machine vision and AI have been applied to electronics inspection. Though solutions can be powerful, they are not truly intelligent. They still rely on humans to discover and characterize problems, provide numerous examples, and custom-code elaborate tests.
This has meant that AI has largely been restricted to large-volume products and limited to production use cases.
Instrumental’s Discover AI is radically different in two key ways:
- It finds new defects on its own. Engineers don’t need to provide examples of anomalies. Discover AI doesn’t just alert you to the defects it’s trained on. It actually proactively discovers new anomalies that might be of interest to product engineering.
- It only takes 30 units to start. Unlike traditional machine vision or AOI, Instrumental can deliver value in early engineering validation builds through ramp and mass production, by constantly finding, categorizing and monitoring defect types even at volumes that would have been prohibitively small before.
Unified data record kickstarts remote failure analysis and correlations across the supply chain
Failure analysis is slow because – even in 2020 – product data remains siloed in multiple on-premise systems, and sometimes isn’t collected at all. Engineers waste hours doing low-value work simply trying to find the data they need to pinpoint the root cause of product issues, before they can work on design or process solutions.
With the introduction of Instrumental Data Streams, product engineers can pull all of their product data – photography, parametric test data, measurements, and more – into a single hub via a simple API to create a complete data history of every unit off their lines. This accelerates failure analysis and enables fully-remote build monitoring and issue resolution from a simple web application.
While Instrumental has provided a real-time image-based data record and AI-powered issue discovery tools to top electronic brands for over five years, today represents a massive expansion of the data Instrumental can aggregate and analyze, delivering an end-to-end product engineering workflow solution for the next generation of electronics brands and manufacturers.
About Instrumental Inc.
Instrumental’s Manufacturing Optimization Platform accelerates time-to-market, improves yields, eliminates rework, and saves engineering time for hardware companies including Motorola Mobility, Lenovo, Axon, P2i, Cisco Meraki, and others.
Instrumental’s cloud-based software proactively identifies issues in real-time as they appear on the assembly line, and provides engineers and manufacturing teams with the complete data record they need to quickly discover new issues, complete failure analysis, communicate concisely with the factory team, and make process improvements in production. Instrumental’s proprietary AI closes the loop from issue discovery to failure analysis, root cause, and corrective action, enabling optimization from anywhere.
Instrumental was founded in 2015 by ex-Apple product design engineers Anna-Katrina Shedletsky and Samuel Weiss.
Related Topics