Are we going to have more robots in the home in the future? Amazon recently announced their first home robot, Astro, after asking this question themselves. This reminded us of the friendly robots that are already working in people’s homes. Robot vacuums like the Roomba or Shark Ninja’s Ion V750 have been around in some form or another since 2002. Tobias and I took a look inside to see how these robots are built and what drives them.
The Shark Ninja Robot is about a foot in diameter with 2 spring-loaded wheels and a floating front bumper. Unlike a lot of vacuums, this one connects to Wi-Fi and even works with Alexa! There are a variety of sensors to detect obstacles and uneven surfaces as it navigates your home. For cleaning, the robot has 2 side-channel brushes and a roller that funnels dust and dirt into the removable dust bin. In a quick demo of how it performs, I turned it on and pressed the dock button and the vacuum made its way to the included charging station.
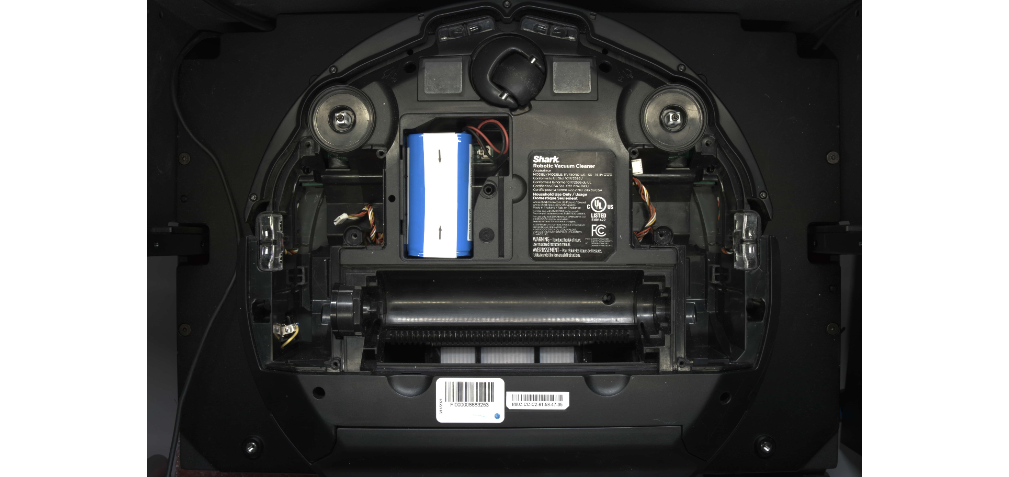
Shark Ion V750 robot with wheels, brush, and battery door removed
I began the teardown by opening up the battery compartment. With only a Philips head screwdriver, any user can access the rechargeable battery for service or replacement. Other components like the main brushes and filter are also easily replaced with simple snap or friction fits. Beyond that, however, the rest of the main housing is held together with T15 and T8 Torx screws. I first removed the two wheels and showed off the spring-loaded mechanism and the first of several motors. We suspected that the wheels were removable because they could be a failure point or need to be cleaned more frequently. Long fibers and hairs often get caught in the wheels and brush of vacuums reducing their speed or range of motion.
From here, I removed the front bumper which allowed me to finish unscrewing the main body of the robot and separate the top housing. With that removed, we were able to take a closer look at the board and other components. What stands out right away is the size of all the components and the array of different wire bundles and harnesses connected to the board. Because the product itself is larger than our previous teardowns, we switched over to the high-resolution photos on the Instrumental platform to get a closer look. Tobias took us through the main components around the semi-circular board including the Wi-Fi module and ARM processor. We also noticed that the different connectors have ink marks on them. These markings could indicate a “first position” indicator to serve as a comparison for service over time or might be a simple way to remember which wire bundle goes with which connector.
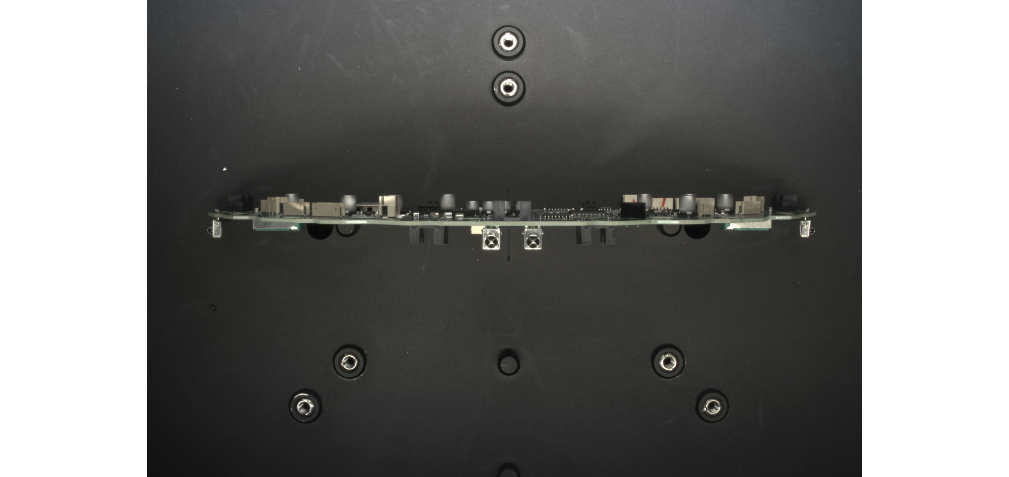
Front view of the main PCBA with IR sensors at the bottom clearly visible
Looking at the board was a great opportunity to ask the audience how the robot actually detects the obstacles in its path. While the answers flowed in, many people identified IR emitters and receivers as the main sets of sensors. This led us to further remove some components on the board looking to find these sensors. We found several on the board but also found a couple of places where no sensors existed at all, just a window! We speculated that this could be because Shark has several models that share the same platform and maybe a higher-end model would include more sensors for more intelligent sensing. Instrumental recently announced a new capability to track High Mix products on factory lines which allows our users to collect data from multiple SKUs and focus on their commonalities to build up a larger data set and identify anomalies faster.
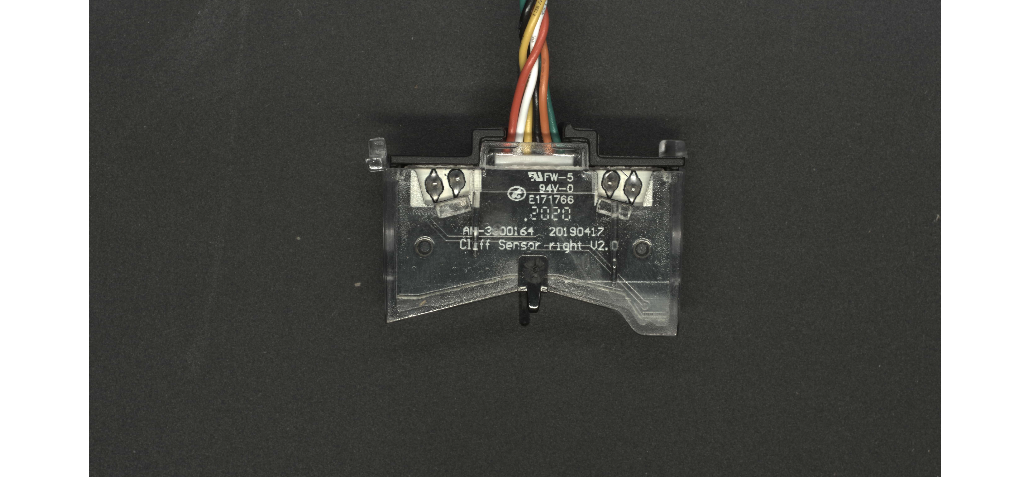
One of several “Cliff Sensor” modules
The Shark vacuum also touts its ability to detect if it will fall down the stairs using proprietary “Cliff Sensors” which we believe to be an IR emitter and detector module pointed toward the ground on the perimeter of the device. The same sensor is used in multiple places in a great example of designing a modular component.
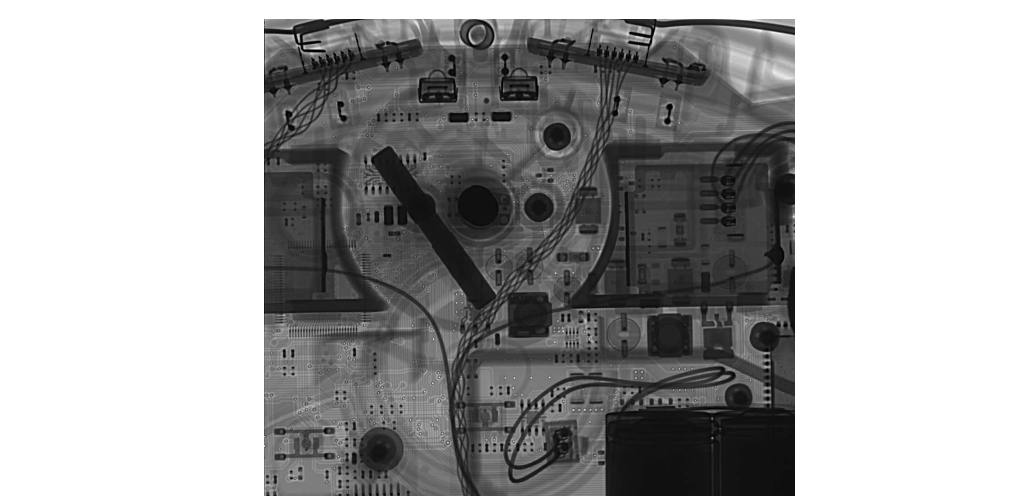
X-ray looking through the front wheel of the device. Note the IR sensors and the boards for the cliff sensors near the top of the image
This was another good opportunity to show off some images from the platform. This time Tobias showed off some great X-Ray views from our partners at Creative Electron. Because the robot was bigger than their typical field of view, they could only take closer crops. Because the device is mostly plastic, a lot of great metallic details showed through including the orientation of the IR sensors, the wiring to all the motors, and the springs for the wheels. Tobias also revealed the way the bumper mechanism works. Instead of physical switches, the Ion V750 robot uses breakbeam IR sensors in the X, Y, and Z dimensions. Depending on how the bumper moves, spring-loaded mechanical beams can interrupt the IR sensor enabling the robot to react and move in a new direction. We think that these sensors provide a high level of sensitivity to any small level of force. Unlike mechanical switches which could wear over time or require a minimum force, these sensors just need to detect minimal movement to trigger.
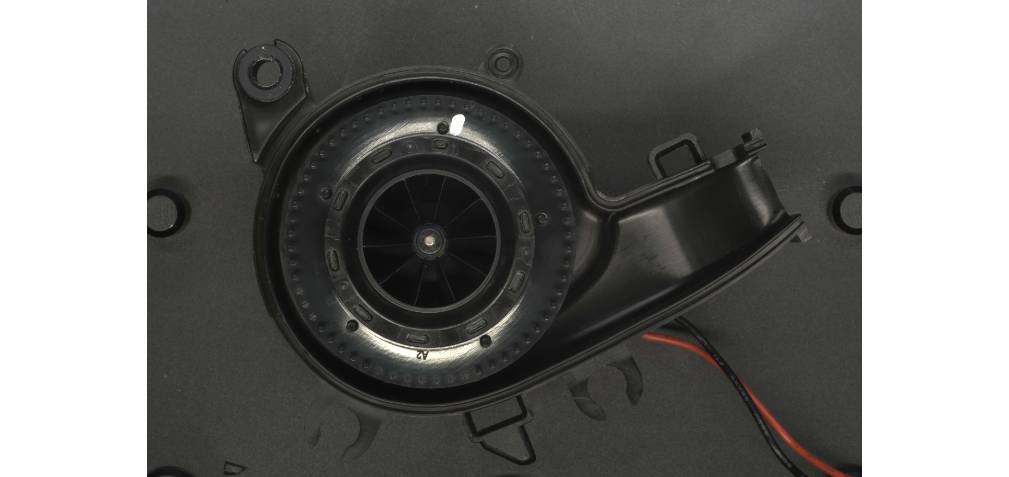
Vacuum impeller with some small plastic ribs removed
To finish up the teardown, I opened up the main vacuum motor assembly. The assembly was secured to the main housing with 3 bolts suspended in rubber grommets for some noise reduction. In addition, the impeller attached to the motor had a lot of little plastic tabs broken off on the device leading to several members of the community suggesting that this was for balancing. This is a common and cost-effective strategy to prolong the life of the motor and reduce unwanted noise or vibration in the system.
While that pretty much wrapped up our teardown, it is interesting to speculate how home robots will evolve in the near future. The random billiard ball approach to obstacle avoidance might work well for a robot vacuum but users will expect more from devices that need to follow them around or navigate more complex environments. More advanced inputs and sensors like computer vision, lidar, and sonar may feed into processors capable of machine learning and artificial intelligence. We can’t wait to see how the home robot evolves and what challenges the designers of tomorrow will need to overcome. If you are working on a next-generation home robot and want to learn more about how Instrumental can help you with your NPIs or mass production, reach out to us at sales@instrumental.com.
Chris Li is a former Amazon Product Design Engineering Manager and current teardown lead for Instrumental. He brought multiple generations of the Kindle to market and advised on the first Echo and Fire TV products. He also worked as the VP of Product Design at the health tech startup, PillDrill, which shipped an award-winning medication tracking system.
Related Topics