Intro
Since 2007, ChargePoint has been creating a fueling network to move people and goods on electricity. With one of the largest EV charging networks available today and a fully integrated portfolio of charging solutions, the company is committed to making it easy for businesses, fleets, and drivers to go electric. The ChargePoint cloud-based subscription platform and software-defined charging hardware are designed to charge any type of EV, anywhere it goes—including passenger cars, delivery vehicles, buses, and more.
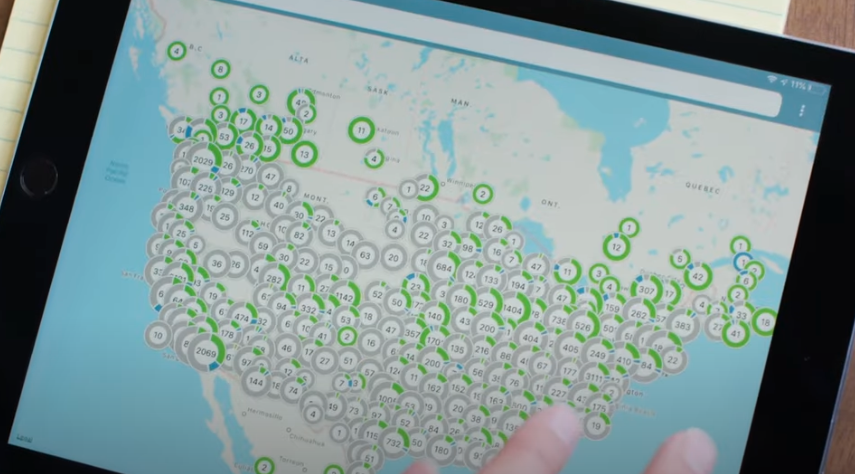
They strive to build a future where going electric is practical but also seamless and reliable. That’s why their focus on reliability and quality is unwavering. They understand the critical importance of ensuring that the charging solutions consistently deliver exceptional performance. Therefore, they take a proactive approach to maintaining the highest standards of quality and reliability.
The ChargePoint operations and engineering teams sought a solution to up-level their supply chain and maintain quality control. That’s how they landed with Instrumental, a Manufacturing AI and Data platform that provides complete data traceability, finds and fixes unknown issues, and gives complete factory oversight. To implement a standardized and scalable process for inspecting each assembly stage, they installed 6 Instrumental Stations across 2 programs.
Results
Using Instrumental’s AI solutions, ChargePoint ensured consistent quality within its EV Charger assembly operations and achieved greater standardization and scalability within its assembly process.
More Productive Development Enabled Higher-Quality EV Chargers
Using AI and referring to the data record, they quickly identified and addressed 17 anomalies during the development phase, preventing potential defects from making it into the final design.
More Efficient and Effective Process and Team
Traceable data and AI-driven analysis expedited issue identification, streamlining problem-solving. This proactive approach saved engineering time and resources.
Without Instrumental, we would have to start looking deeply at the earlier assembly processes. Using Instrumental reduced our defect hunt [and root cause] time by half.
- Ali Mansour, Technical Program Manager
Read the full case study to learn more.